ROTOGRAVURE (GRAVURE)
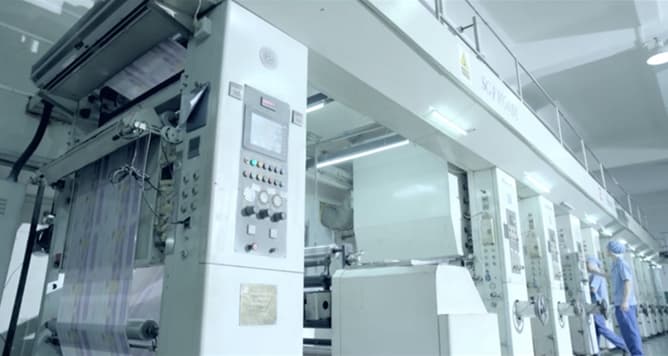
- 9 Gravure presses available
- Short print runs
- Low origination costs
- Short lead times
- Photo quality print
- Recyclable films available
Rotogravure utilises Copper plated steel cylinders which are laser photoengraved and hold the ink ready for transfer to the substrate. Because gravure is capable of transferring more ink to the substrate than most other printing processes, it is noted for its remarkable density range (light to shadow / vignette) and hence is a process of choice for high quality image reproduction.
Advantages
Gravure has the ability to print on thin film such as polyester, polypropylene, nylon, and polyethylene, which come in a wide range of thicknesses, commonly 10 to 30 micrometers.
- Printing cylinders that can last through large-volume runs without the image degrading
- Photo quality image reproduction
- Can print on virtually any substrate including recyclable films
- Low per-unit costs running medium-high volume production
- Specialist low volume presses available from approx. 100kg or 10,000pcs.
- Solvent-based inks
- Water-based inks (commonly used by FMC Packaging)
- Ultraviolet inks
- Low origination / cylinder costs (Exclusive to FMC Packaging)
- Short print runs 100kg-250kg (Exclusive to FMC Packaging. Excluding recyclable films)
Disadvantages
Shortcomings of the gravure printing process include:
- Start-up costs: tens of thousands of copies needed to make it profitable
- Lead time for cylinder preparation when compared with Flexographic, Offset or Digital
- Slower print speeds when compared with Flexo, approx. 400 meters per minute.